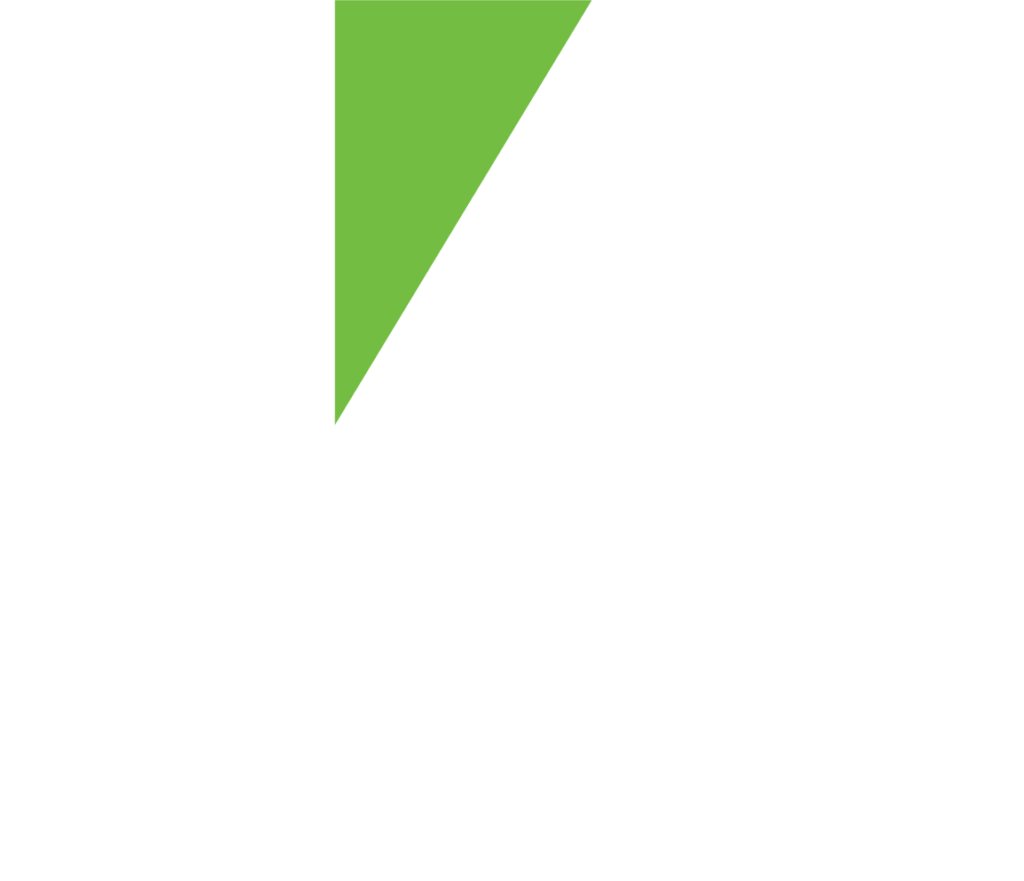
With Spray Foam Application, Temperature Matters.
When installing spray foam insulation, temperature matters. Environmental conditions, particularly temperature, play a critical role in the success of the project. The type of spray foam you choose, along with how well it cures and adheres, can be significantly affected by the environment. For contractors, understanding how these factors interact is essential to achieving a durable and effective insulation solution.
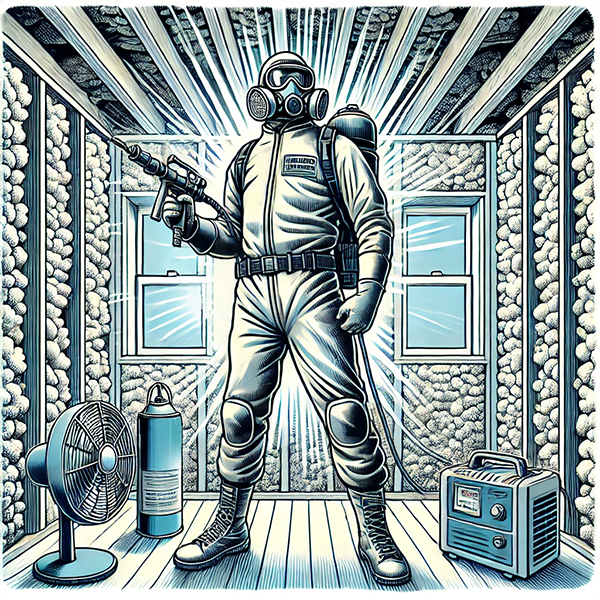
THE SCIENCE OF SPRAY FOAM MIXING AND TEMPERATURE
Buckle up — let’s put on our lab coats and get geeky for a moment.
Spray foam is created through the combination of two chemicals: isocyanate and polyol resin. These components are kept in separate tanks and only mixed at the point of application. The chemical reaction between them generates the foam that expands and hardens. However, for this reaction to happen properly, temperature is key.
Ideal ambient and substrate temperatures for spray foam application are typically between 60°F and 80°F (15°C to 27°C). In colder temperatures, below 60°F, the chemical reaction may slow down, causing poor mixing, reduced expansion, and inadequate adhesion to surfaces. When this happens, the foam may not cure properly, leading to voids or reduced insulation performance.
On the other hand, high temperatures can cause the foam to cure too quickly, leading to inconsistent application. The foam may become too rigid, preventing it from expanding to its full potential. Additionally, applying spray foam on surfaces that are too hot can cause blistering or delamination, weakening the insulation.
CHOOSING THE RIGHT SPRAY FOAM FOR THE CONDITIONS
Contractors should carefully select the type of spray foam based on environmental conditions. Closed-cell spray foam is more tolerant of temperature fluctuations and provides higher R-value, making it a good choice for colder climates. However, in very cold weather, special winter-formula spray foam is recommended to ensure proper curing. Open-cell spray foam, while more flexible and breathable, should be used in milder conditions where temperature and humidity are less of a concern.
NEGATIVE IMPACTS OF POOR TEMPERATURE MANAGEMENT
Improper temperature management can result in foam shrinkage, cracking, and loss of adhesion. This not only reduces the insulation’s effectiveness but can also lead to costly reapplications. For example, in cold temperatures, foam that doesn’t expand fully may leave gaps that allow heat transfer, negating the intended energy savings.
BUT WHAT'S IT ALL MEAN?
For contractors, environmental factors like temperature are crucial to the successful application of spray foam insulation. Whether you’re using open-cell or closed-cell foam, ensuring the right conditions for mixing and curing can help you deliver quality results that last. Always be mindful of the temperature and choose the appropriate type of spray foam to avoid common pitfalls like shrinkage or poor adhesion.
Need help choosing the right spray foam for your job? Give us a call!
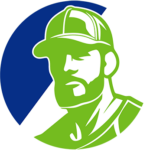
PRO TIP:
- If heat is required to warm the project, make sure to use dry heat (indirect heat, electrical, or wood heat are best). Direct burning of fossil fuels for heat can add unnecessary moisture to your project.