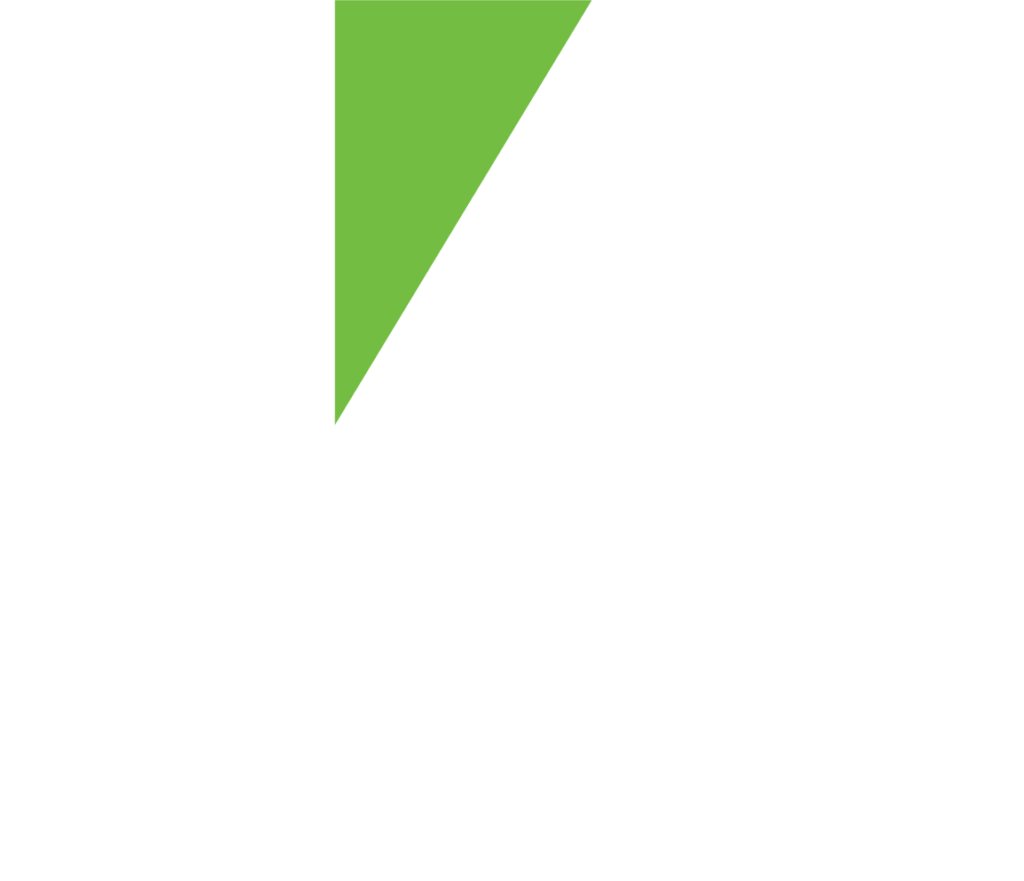
Ain’t Nobody Got Time for Worn Insulation Blowing Hoses
We all know maintaining equipment is important. But perhaps it’s because you can operate an insulation blow machine with a worn hose, some contractors do. The hard truth is: waiting until a hose is on its last legs is a bad plan. Here’s why.
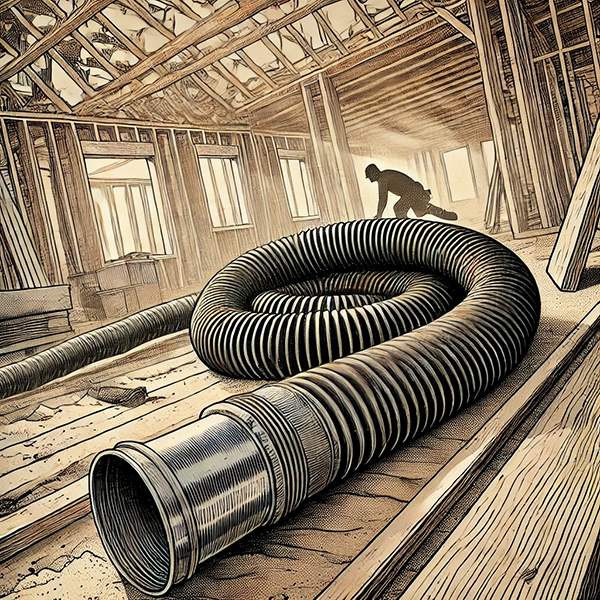
THE PAINS OF WORN INSULATION BLOWING HOSES
Insulation blowing hoses play an important role in spreading out the insulation. A worn hose does this less well. The insulation reaches the home too tightly packed and doesn’t cover as much area. Which means every single job installed with a worn blowing hose requires more bags of blown than it should. Insulation manufacturers report that a worn hose can reduce insulation coverage by at least 15 and as much as 20%. Independent testing has confirmed those results. Doing the math, when an installer is using a worn hose, they may need to install up to 20% more product to meet the desired R-value for the project. A job that should have taken 10 bags of blown now needs 12. We all like paying for, hauling, and installing more insulation than needed, right?
NOT JUST A HOSE
Loose fill insulation starts in a highly-compressed package that needs conditioning. This conditioning occurs both mechanically in the blowing machine (machine settings equally important) and as the product flows through the delivery hose. The ribs inside the hose condition/open the insulation fibers for proper thermal results in the attic spaces. As hoses age, the ribs inside wear down, limiting the effectiveness of the fiber conditioning. Simply put, using a worn hose reduces the quality of the insulation coverage.
COST-EFFECTIVE REPLACEMENT
A worn hose replacement pays for itself in no time. Losing 15-20% of profitability on every job with a worn out hose is an easy calculation to justify the replacement cost. Investing in a new hose can easily save you more in the long run by ensuring high-quality insulation coverage on every job. At Performance Pro Supply, we can get you a great price on replacement insulation blowing hoses, other replacement parts, and anything you need for blown-in insulation.
WHEN TO REPLACE INSULATION BLOWING HOSES
How can you know when it’s time? Feel inside the hose. If the ribbing feels worn down, it’s not doing its job like it should. Another simple way to check for wear is to squeeze the hose. If it easily deforms out of its round shape, its hoop strength is compromised. In either case, it’s time for a new insulation blowing hose.
A general rule of thumb is to replace your insulation blowing hose between 6 and 12 months. Daily users will want to replace at the 6-month mark. Regularly inspecting and replacing worn hoses is a small investment that pays off. Contact Performance Pro Supply today to replace your insulation blowing hoses, get other replacement parts, or anything else needed to install blown-in insulation.
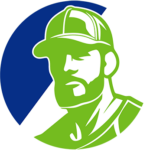
PRO TIPS:
- Set up a hose replacement program to maintain highest performance results. Purchase a new hose every 6 months.
- Flip the hose after 3 months. Reversing the hose equally wears down the ribbing in both directions, ensuring you maximize its useful life.